
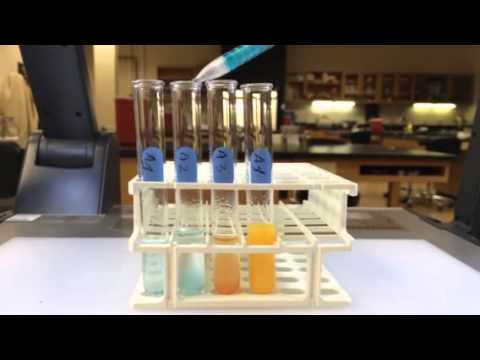
The experimental values of the drawing forces along the entire drawing route are shown in Table 5. In this experiment, the average value of the drag force is 3050 N. The presence of a large number of measurements of the drag force per second, which is more than 600 points per second, allows the calculation of the average value. This is due to a change in the friction conditions in the deformation zone, the cause of which may be a different quality of the wire surface preparation along the length and an unsettled flow of technological lubricant into the deformation zone. As can be seen on the curve ( Figure 8), the value of the drawing forces changes from the maximum value of 3650 to the minimum value of 2750 N. Measured on a laboratory drawing machine and obtained by drawing the wire in pass 3 (wire diameter 3.20 mm), the drawing force data are shown in Figure 8. Ī comparative analysis of the drawing forces obtained experimentally during the drawing on a drawing machine ( Figure 1) and the calculated values ( Table 4) was carried out to verify the developed mathematical model.
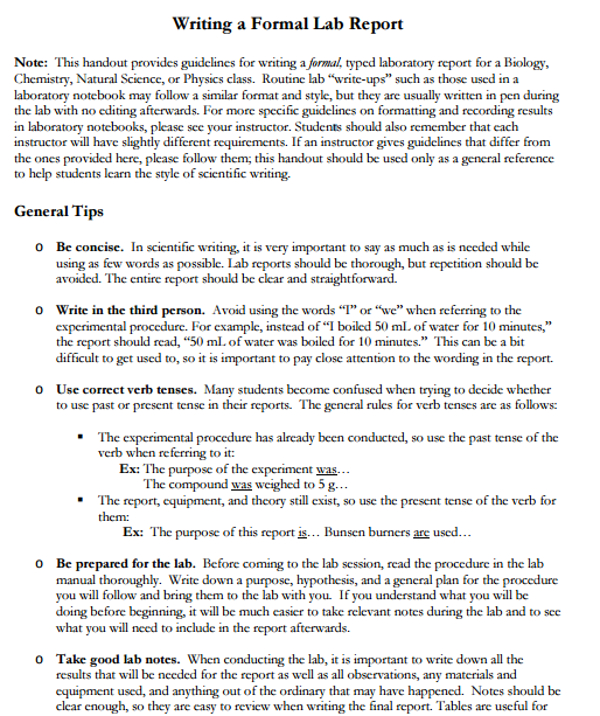
The straight-line principle of high-speed wire drawing introduces its own characteristics into the methods for constructing drawing routes and estimating the energy-power parameters of the process. The high level of automation of modern drawing equipment has made it possible to increase the drawing speed in dry wire drawing from 8 m/s to 40 m/s, which in turn entails a change in requirements for lubricants, the quality of preparation of the wire surface and drawing tools. Significant changes with the introduction of straight-line drawing machines are associated with an increase in drawing speed. The transition from the pulley-type continuous wire drawing machine to the straight-line wire drawing machine has led to a change in the technical and technological parameters of the drawing process in a monolithic die. However, monolithic drawing remains the most common and frequently used method of wire production. This makes it possible to replace sliding friction with rolling friction between the tool and the wire, which reduces the drag force and allows large single strains to be applied per pass. Alloys such as stainless steels and titanium alloys, which are difficult to work with monolithic drawings, are plastically deformed in roller dies. Drawing can be carried out through monolithic, and roller dies. Drawing is the most common method of making wire. The wire is produced by such metal-forming processes as rolling, extrusion, drawing and their combination. To improve the accuracy of the developed mathematical model, it is shown that in the future, it would be necessary to conduct experimental studies on a laboratory drawing machine to determine the effect on the energy-power parameters of the drawing process of the values of technological parameters entered into the program as constant real values, such as the friction coefficient, die half-angle, drawing speed, and back tension. A change in the friction coefficient by 0.02 when drawing nickel wire leads to an increase in stress and drawing force by 20%. Experimental studies have been carried out to determine the energy-power parameters of nickel wire drawing on a laboratory drawing machine with an installed ring strain gauge to determine the drawing force. The calculation of energy-power parameters of drawing nickel NP2 (Ni 99.6) wire ∅1.8 mm from ∅4.94 mm wire rod is given. The equations of hardening during nickel NP2 wire drawing are obtained. To select the technological parameters of the deformation zone, which ensure uniform deformation over the wire cross-section, a nomogram was compiled. The developed mathematical model differs in that it allows us to evaluate the uniformity of deformation over the wire section, depending on the technological parameters of the deformation zone, namely, the semi-angular die, the coefficient of friction and the degree of deformation.
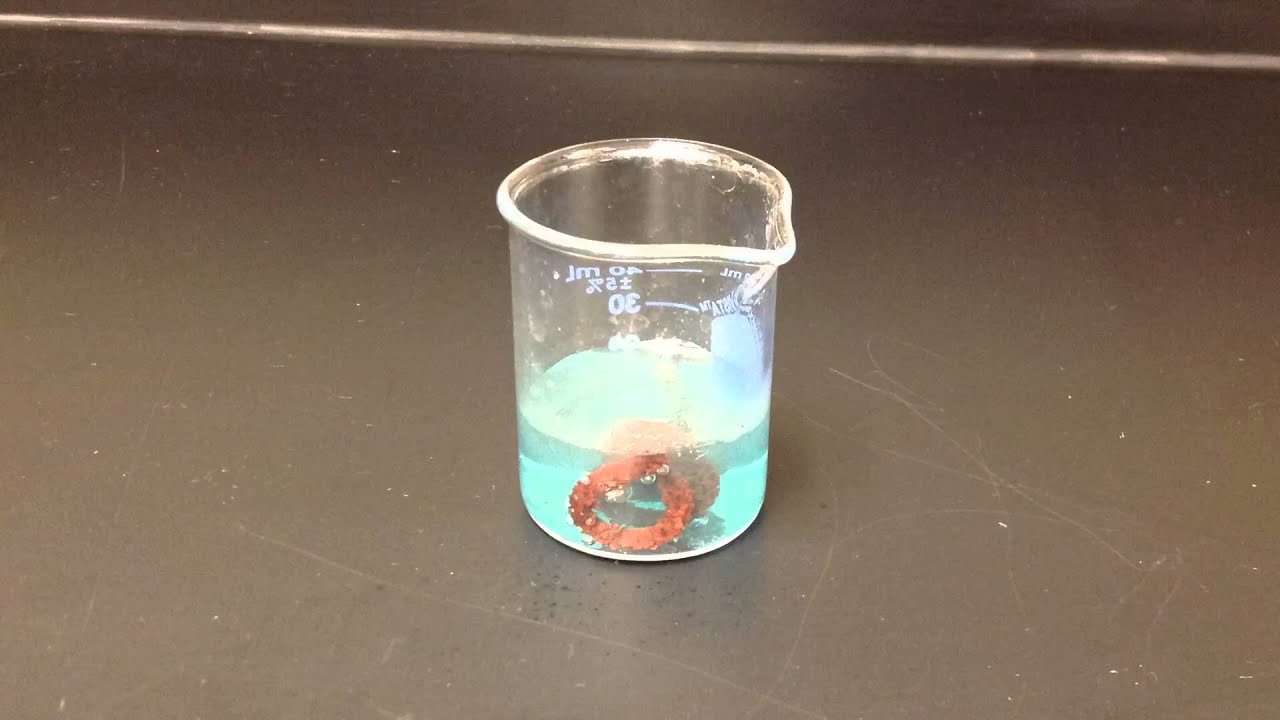
The program allows us to calculate drawing stress, drawing force, tensile strength and yield strength of the alloy after wire drawing, safety factor, and drawing power. In this article, a mathematical model has been developed for calculating the energy-power parameters of the drawing process in monolithic dies on straight-line drawing machines, and its adequacy has been validated in experimental wire drawing on a laboratory automated drawing machine.
